A great soldering iron opens up a world of tinkering possibilities—it lets you melt, mend, and reshape the “glue” that holds electronics together. Here at iFixit, we’re unabashed iron nerds! We’ve spent years refining our new Smart Iron, and we’re excited to share what we’ve learned about one of the most critical (and overlooked) parts of an iron: the tip. We designed the Smart Iron soldering tip to perform at 100 watts while maintaining a precise temperature—something that’s impossible to do with existing designs. A well-designed tip can make all the difference between a smooth solder joint and a messy meltdown, so let’s dive into the world of tips!
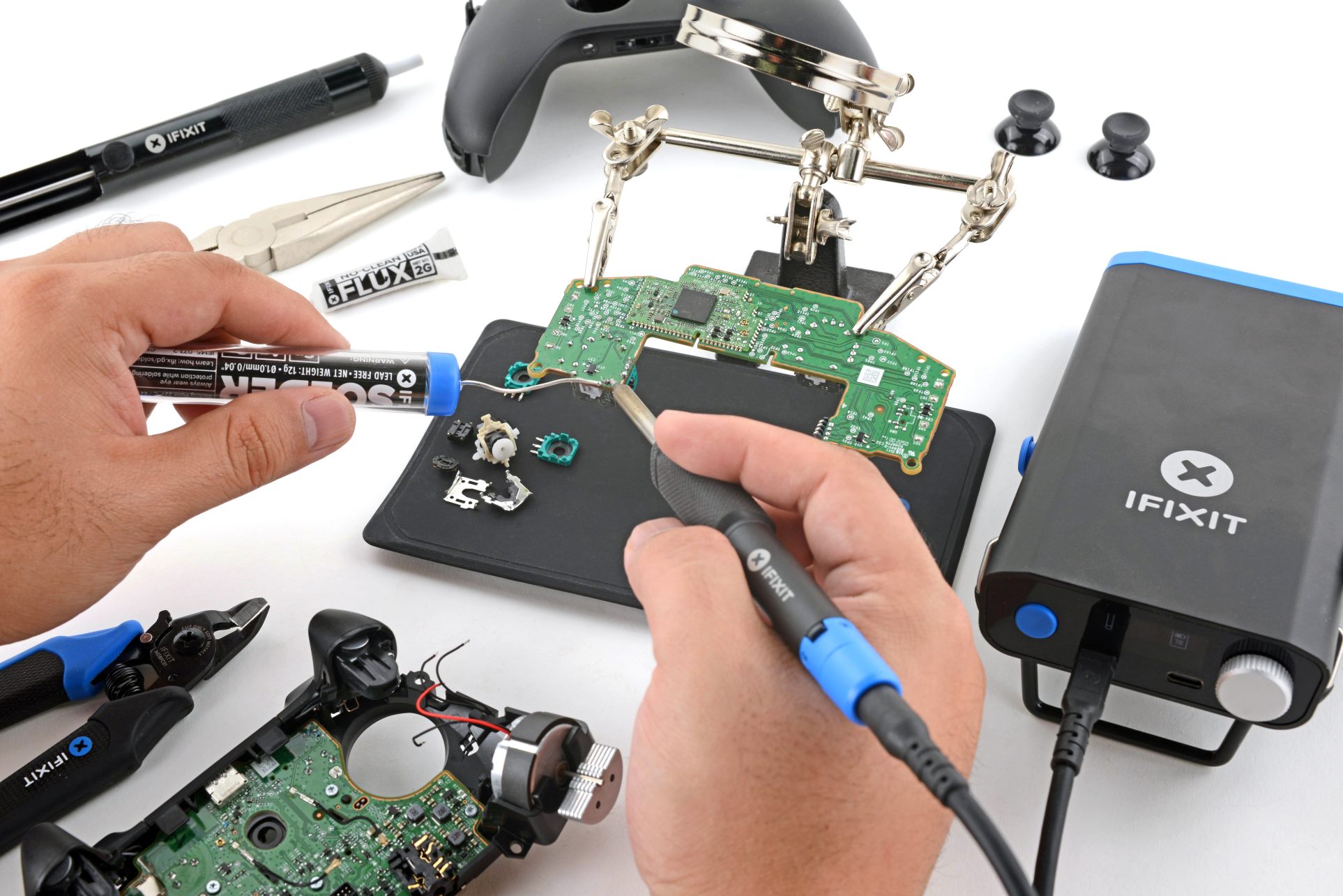
We’ve Got a Hot Tip for You
Soldering iron tips have evolved dramatically over the years. The earliest irons were a heavy block of metal that you heated on a fire or oven. Then, manufacturers started integrating electric heating elements. As electronics got smaller, these designs shrank into the sort of soldering iron that we’re all familiar with today. But these irons had an Achilles heel: over time, the tip of a soldering iron naturally oxidizes—and once that oxidation builds up, heat transfer suffers and solder no longer flows smoothly. Early soldering irons were built as a single unit, so replacing the entire iron was the only real way to fix a badly oxidized tip. To solve that hassle, manufacturers introduced replaceable “cone” tips. Instead of tossing out the whole iron whenever the tip got gunky, you could simply swap in a fresh cone, restoring optimal heat transfer and extending the life of your tool. This modular approach paved the way for more specialized tip shapes and materials, further improving the soldering experience.
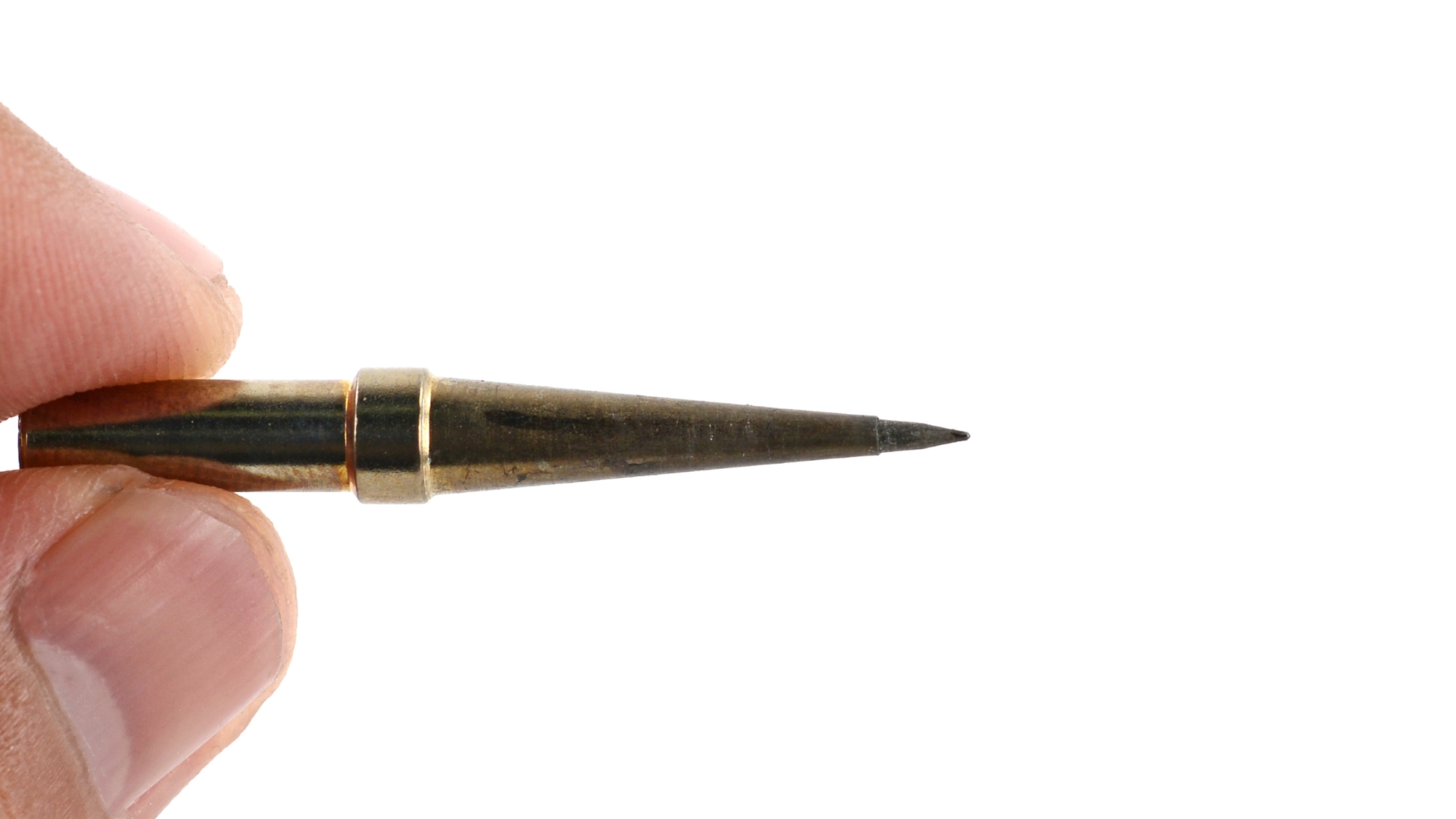
Next, manufacturers introduced temperature feedback, often by embedding a thermocouple inside the heating element—improving accuracy, but still not delivering the speed or precision many advanced jobs require. Today, modern soldering irons integrate the heating element and temperature sensor directly into the tip itself. This tight coupling, managed by intelligent software, gives these irons remarkably fast heat-up times and pinpoint temperature control, ushering in a new era of precision soldering.
You can see this in action in this CT scan cutaway of our Smart Iron tip here:
From the beginning, we wanted to build a high power, incredibly responsive iron comparable with the highest end wall-powered irons on the market. When we started our work on the FixHub, we also wanted to use standard connections instead of the proprietary systems you see in most tools. We’re strong believers in reusability and modularity. Rather than using a proprietary battery pack or cable to a fixed soldering station, we designed the system around USB-C since it was an industry standard that all of us are already using.
We started out thinking it would make sense for our new iron to also use the same tips as other irons on the market. The old-style ‘dumb’ tips wouldn’t work, but there were new tips with built-in heaters from a few manufacturers worth considering. The most popular is probably the T12 tip from Hakko. We explored designing an iron compatible with these existing tips, but couldn’t find any that met all of our design requirements. Why did we decide to do the extra work to develop our own tips? There were a lot of factors, but here are the top three:
- We wanted to create the most ergonomic soldering iron ever made, and existing tips didn’t fit the size and shape that we were looking for–they were all too large. Our goal was to create an iron that felt as natural in your hand as a pen. That led us in the direction of an iron with a much shorter tip than other options on the market.
- None of the tips on the market met the electrical characteristics that we needed for a high-performance, USB Power Delivery-native 100-watt iron.
- No technical standards exist for a ‘smart’ soldering tip with an integrated thermocouple and heater. There isn’t a technical standard defining iron tips, and the real-world performance of tips is all over the map.
Fit, Finish, and Balance
We started working on our iron by focusing on the design. We were frustrated by the form factor of existing tiny irons like the Miniware TS100 that were uncomfortable to use for more than a few minutes.
The Smart Iron’s pen-like form factor was the culmination of countless prototypes and meticulous refinements. We tested different materials, diameters, and grip finishes in our quest for a soldering iron that felt natural in your hand, even during marathon work sessions. Our goal was to strike a balance between stability and maneuverability: solid enough to work a variety of materials, yet light enough to grip for detailed work without tiring out your wrist.
Rather than feeling bulky or awkward in your hand, the slim, elongated body more closely resembles an everyday writing instrument. This design makes precision work much easier—especially during delicate soldering tasks that require careful positioning and a steady grip. The handle accommodates a comfortable, ergonomic grip so you can spend long stretches soldering without hand fatigue.
During each iteration, we iterated on the iron’s center of gravity and ergonomics. If the grip was too thick, it felt clumsy to maneuver; if it was too thin, it became painful to hold for extended work. Through trial and error, we found that “just right” diameter and weight distribution that lets your fingers rest comfortably around the handle without feeling cramped or strained.
We agonized over the surface texture—glossy finishes can be slippery, but overly grippy rubbery coatings can snag on sleeves or work surfaces. We settled on a gentle matte finish that offers traction without feeling tacky. It’s not just about looks, either. The final shape and finish keep the iron from rolling off your desk and help you effortlessly pivot your hand for precise movements. By the time we landed on the final design, we knew we had something that combines comfort and control in a way that legitimately enhanced the soldering experience.
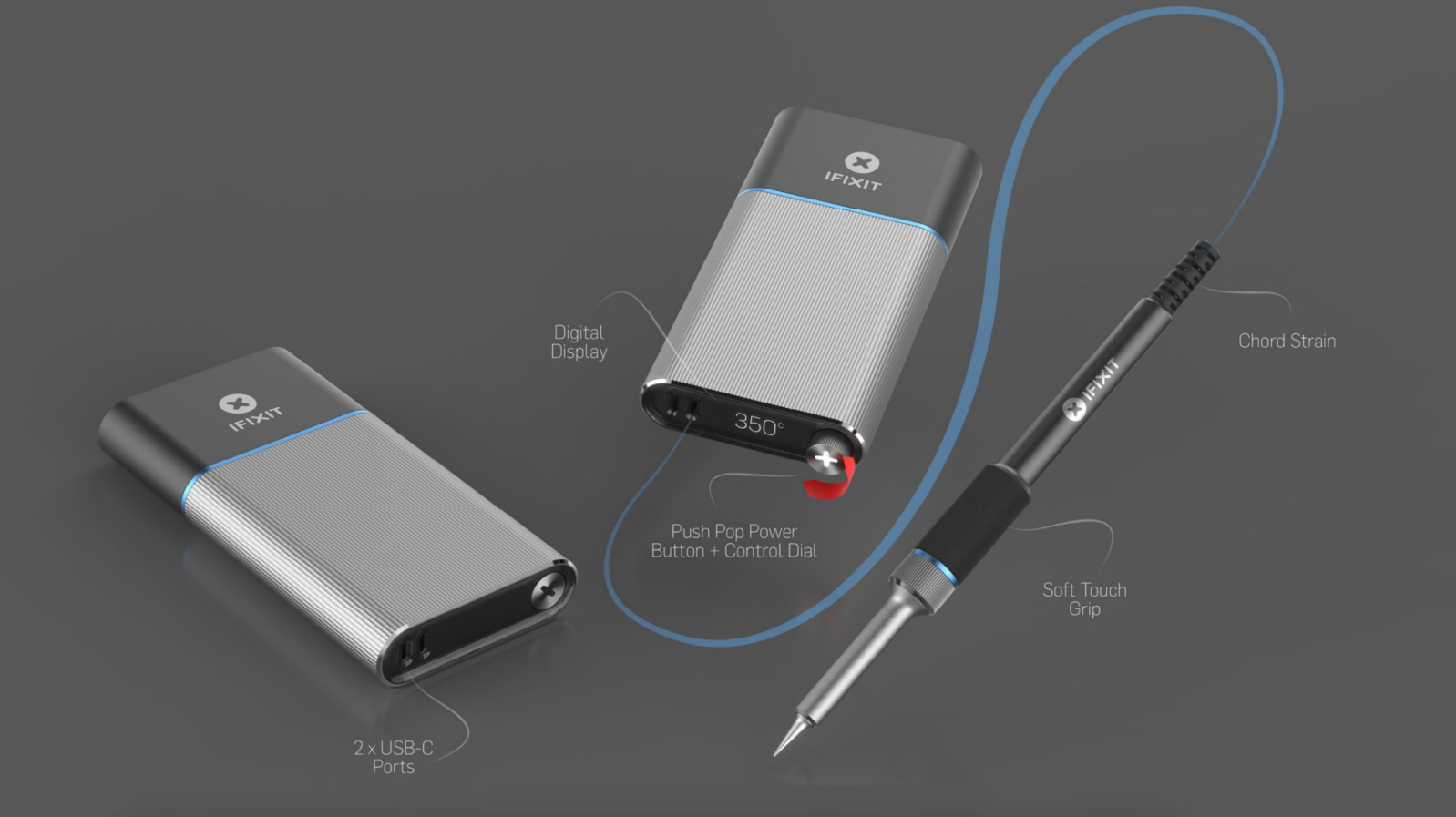
An early design mockup of the FixHub Power Station and Smart Iron.
At the heart of this pen-like form factor is a straightforward ⅛” TRS heater tip assembly that slots neatly into the front of the iron. Because the heating element and thermocouple are integrated into the tip, everything remains self-contained—no extra hardware bulking up the handle. It’s a design choice that not only speeds heat-up times and improves temperature stability, but also keeps the iron’s center of gravity well-balanced. You’ll feel like you’re handling a fine marker rather than a piece of heavy equipment.
I Need More Power, Scotty!
Taking full advantage of the USB Power Delivery specification required a tip resistance not present in other soldering irons on the market. When we set out to design a 100 W soldering iron that runs from a 20 Volt USB-C source, we quickly discovered that most existing soldering tips have too high a resistance. The tips Pinecil uses, for example, are either 6 or 8 ohms. We want to run as much current through the heater as possible to take advantage of the power provided by USB Power Delivery, but with an 8-ohm tip, we’d be stuck below 50 W, well below the performance we’re aiming for. (The formula, for those of you who want to double-check our math, is P = V2 / R.) By lowering the tip’s resistance to 3 ohms, we can draw enough current to hit our 100 W target, even with some voltage loss. Less resistance means more power at a given voltage. Since we couldn’t find any off-the-shelf tips that fit this requirement, we developed our own—crafting a 3-ohm tip that can fully tap into a 100 W USB-C supply.
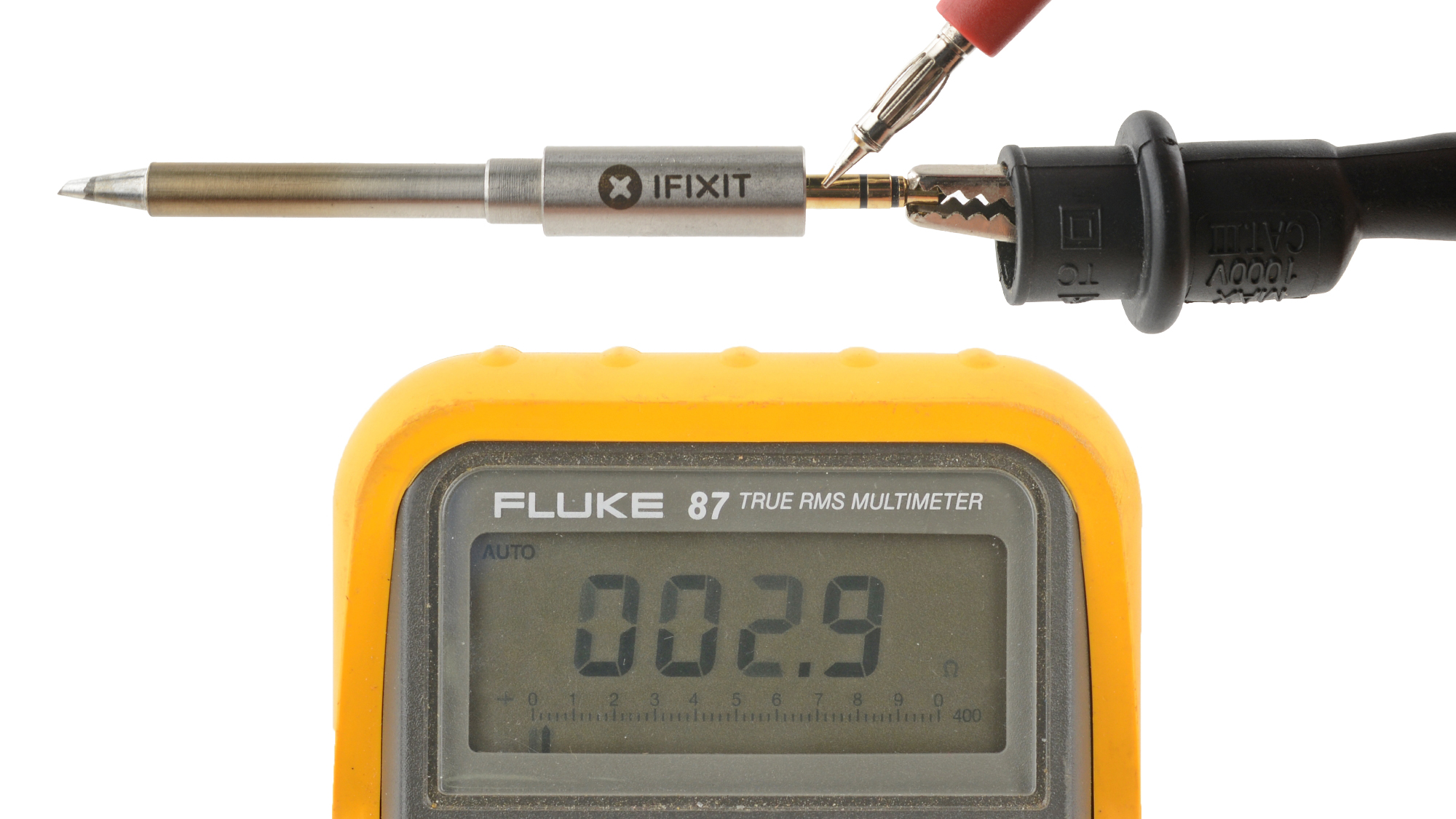
Now, I know all of you circuit designers are saying, “You don’t have to stick with 20V! You can boost the power.” Yes, we could have ramped up the voltage with a buck-boost converter, but that would have added size (the buck boost converter circuitry that we use in the Power Station took up 1” x 0.75”, too large to fit in the handle) and heat to the handle that we deemed unacceptable. Engineering is all about tradeoffs.
What’s in a Connector?
Once we decided that we’d have to make a new tip for electrical reasons, we had a chance to rethink the connector. After searching the world for compact, durable connectors that could handle 100 Watts, we selected one of the most universally available connectors in the world: the venerable 3.5 mm, or ⅛”, headphone jack. It can handle our current load, is super rugged and robust, and is widely available in the market. It strikes a balance between our specialized electrical needs and a standard plug type.
This means our tips won’t drop into other irons, and that’s not ideal. But our design isn’t proprietary–we haven’t patented it, and anyone that wants is welcome to use this form factor.
Unlike the widely adopted USB-C connections found throughout FixHub, the connection between a soldering iron tip and its body is not regulated by any standards body. Each major manufacturer employs its own method for connecting cartridge tips to their soldering irons, either through entirely custom assemblies or by combining standard connectors with a heater core–like we did with the ⅛” stereo jack.
One other factor that we considered: When a particular soldering iron technology becomes popular, aftermarket or unlicensed manufacturers often reverse-engineer compatible tips for the original soldering irons. Sometimes they create great products, and sometimes they cut corners on quality and performance. That’s the nature of the aftermarket. Because there’s no technical standard, it would have been very difficult for us to provide a consistent experience (or temperature) with these tips. In our tests, the consistency and quality of these aftermarket tips vary wildly.
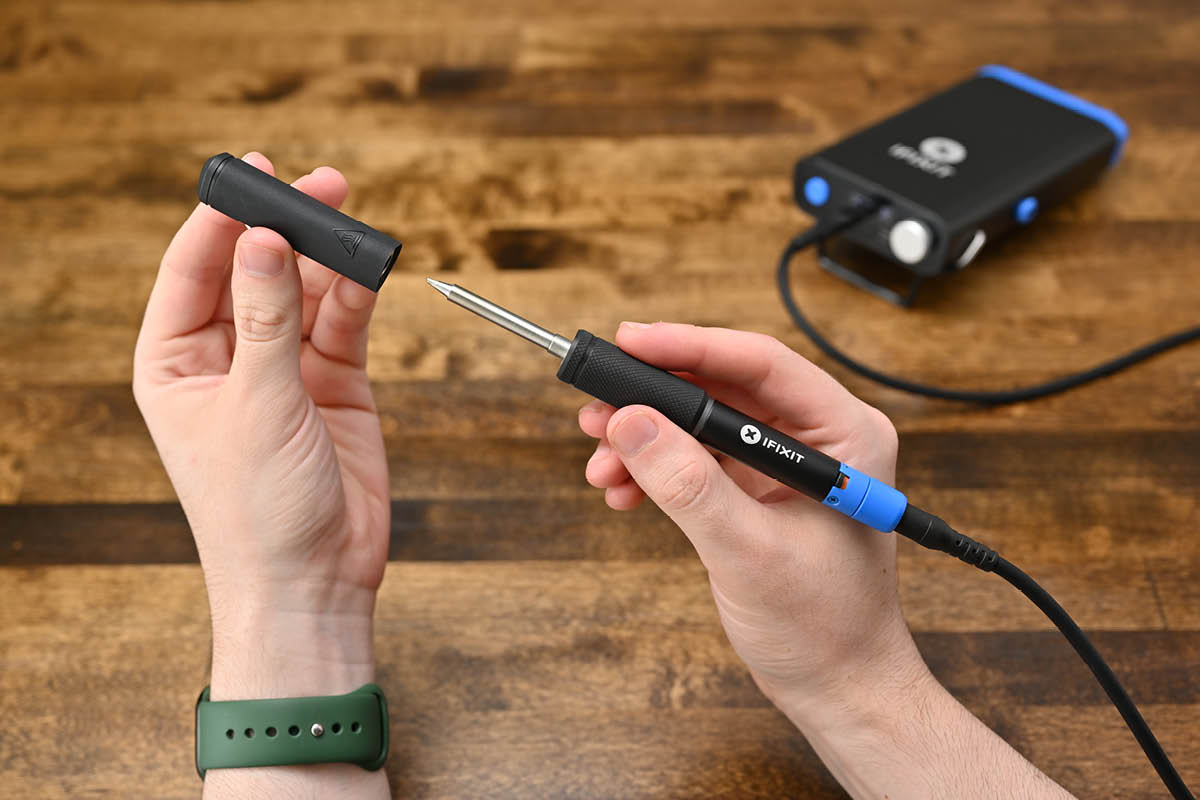
A World of Tips
There are a whole world of soldering tips out there, from Hakko’s popular T12 / T15 to JBC’s ceramic core tips. Hakko, a Japanese company whose quality products we have sold for a long time, revolutionized soldering with their patented, cartridge-style tips in the early 2000s. By the time 2015 rolled around, the success of these Hakko-style tips inspired Guangzhou-based Miniware to make a soldering iron handle compatible with these tips. Miniware eventually started making their own tip shapes, but still with the Hakko connection. Since then, countless factories have replicated the design, and fragmented the market with a wealth of options of widely varying quality.
This trend isn’t limited to Hakko; the Aixun T3a soldering station utilizes JBC tips (as do several others), and you can see how original designs are often borrowed or altered.
Miniware TS100 and Pinecil use Hakko-compatible tips that come in a variety of resistances. In practice that means it’s a little bit of work to figure out what power each tip is capable of–and temperature accuracy is all over the place. Pinecil has a wiki with extensive details to help their customers identify the resistance and version numbers of each tip. We wanted to dodge that complexity and make sure that people could always feel safe and confident of the output power when using our iron.
The FixHub Smart Soldering Iron is engineered to deliver higher wattage over USB-C than any other soldering iron on the market. To ensure safe operation, we maintain tight control over tip resistance.
There’s one other reason that we couldn’t use off-the-shelf tips: standards compliance. Our iron meets strict UL and IEC-certification and has passed safety lab TUV Rheinland’s rigorous standards, something that we couldn’t readily do if we claimed to be compatible with, for example, Hakko T12 soldering iron tips. Other irons without safety certifications, like the Pinecil and TS-100, cannot be sold at most retailers in the US and Europe.
Designing a Tip that Lasts and Lasts
One of the biggest tip killers is oxidation, which occurs when the metal tip reacts with oxygen in the air. At high temperatures, this reaction accelerates, forming a layer of oxide on the surface of the tip. This oxide layer is a poor conductor of heat, making it harder for the solder to flow properly and reducing the efficiency of your work. Over time, severe oxidation can render the tip unusable, forcing you to replace it.
The Smart Iron’s automatic sleep sensor mitigates this problem by lowering the tip’s temperature to an “idle” zone after 30 seconds of inactivity. This significantly reduces the interaction between oxygen and the tip, slowing down oxidation and preserving the tip’s lifespan. When you’re ready to resume work, the iron heats back up to soldering temperature almost instantly, allowing you to dive right back into your project without delay. Thanks to this drop-and-resume approach, you’ll replace tips far less frequently compared to other irons that stay hot continuously. We’ve launched the Smart Iron with six tips: Cone, Bevel 1.5, Wedge 1.5, Point, Bevel 2.6, Knife 2.5, Knife 1.4. We don’t plan to stop there, but need your input on what’s useful. What tips should we make next?
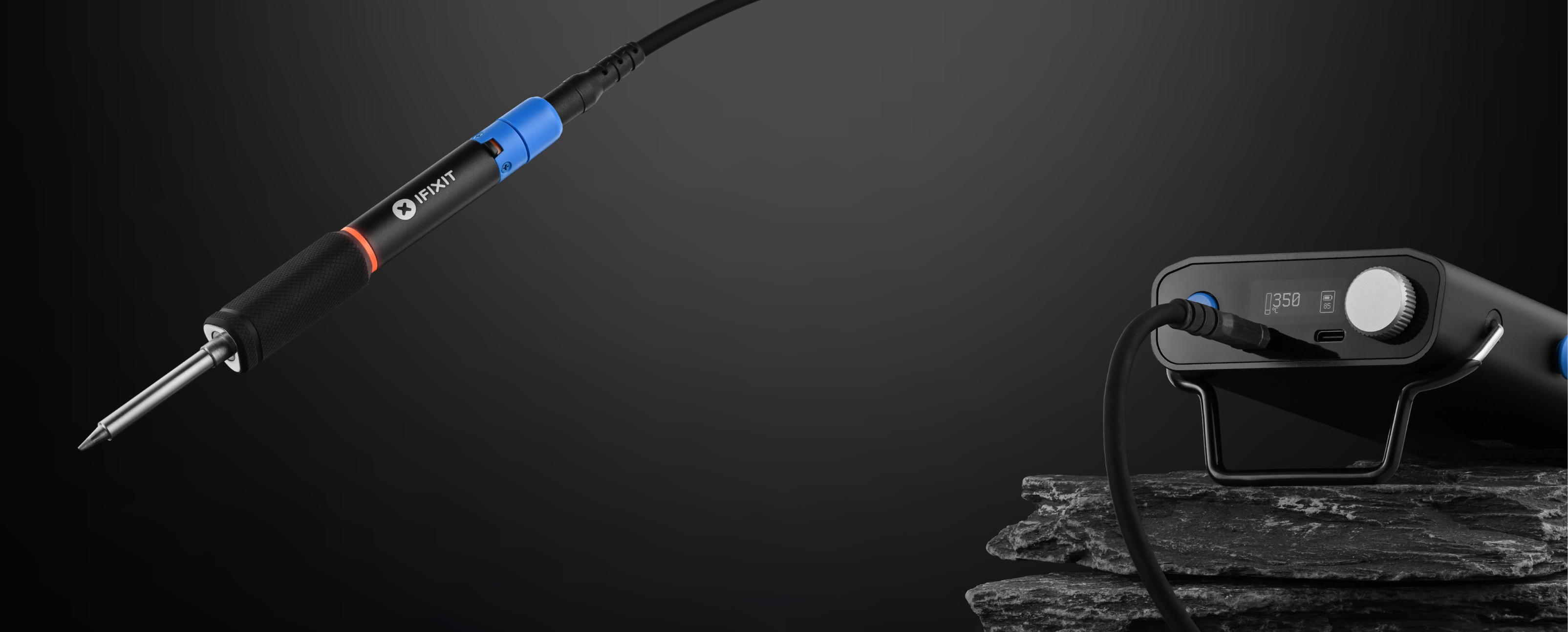
5 Comments
CNC kitchen makes a heat-set insert remover, any chance y'all will make a tip that enables compatibility?
Peter - Reply
@wazbaz, I been waiting for a tip compatible with CNC Kitchen's heat set insert tip sets, ever since iFixit announce their iron. If iFixit make a tip for the insert sets, it will be compatible with the remover as well, since they all use a M5 thread.
Jonathan Yao - Reply
A hooked tip similar to the J02 for the TS80P would be an amazing addition to the lineup.
Alex T. - Reply
I'll echo the call for a heat set insert tip.
Doug Smith - Reply
Thanks for the heat set insert tip idea, I think that makes a lot of sense. We'll take a close look at it!
Kyle Wiens - Reply